Forming, Finishing and Packaging Services
Production Metal Stamping and Punching:
Metal punching is used to create a desired shape in a part that is already produced while metal stamping is used to create the profile of a part in its entirety. We utilize our punching process alongside our laser-cutting and wire EDM processes to produce a high quality precision product efficiently. Metal stamping is recommended for high volumes while Metal punching is recommended for lower volumes.
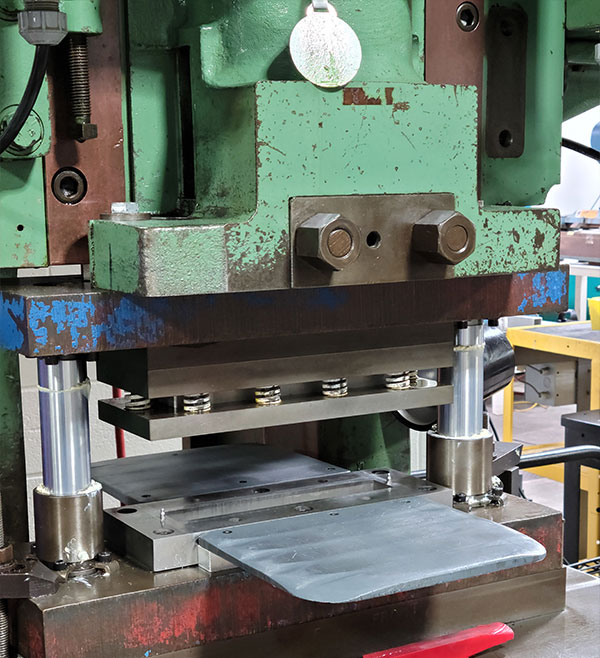
Heat Treatment Services:
Metal heat treatment is often used to harden and soften metal. By doing a heat treatment to a part, it can be used to increase the strength of the material.
At Grace Manufacturing, our heat treatment has a big focus on the medical and aerospace industry. We offer vacuum heat treatment of a variety of stainless steels as well as tempering. Heat treating products at a vacuum and quenching with Nitrogen gas produces a clean, consistent finish appropriate for medical devices and other critical products
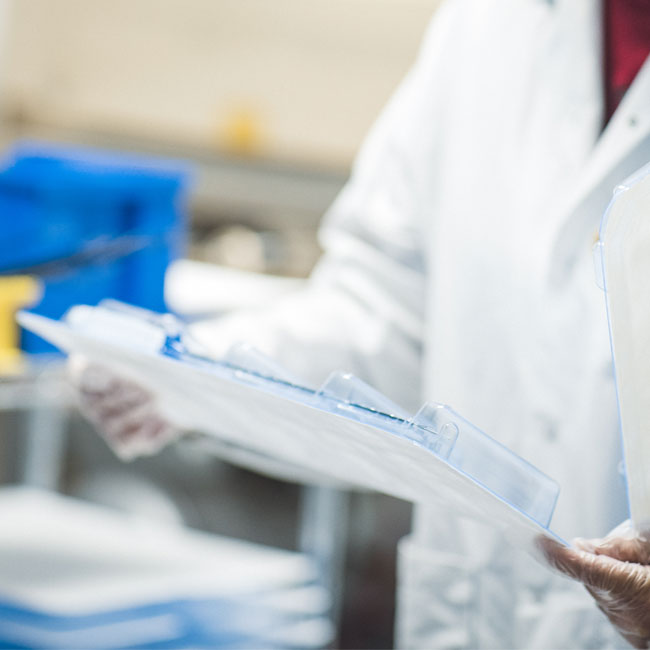
Finishing Services
- Vibratory Finishing: Can be used on a variety of products to create a consistent matte finish. We currently use this process for medical products as well as contracted job-shop parts. We recommend this process for larger parts with high volumes
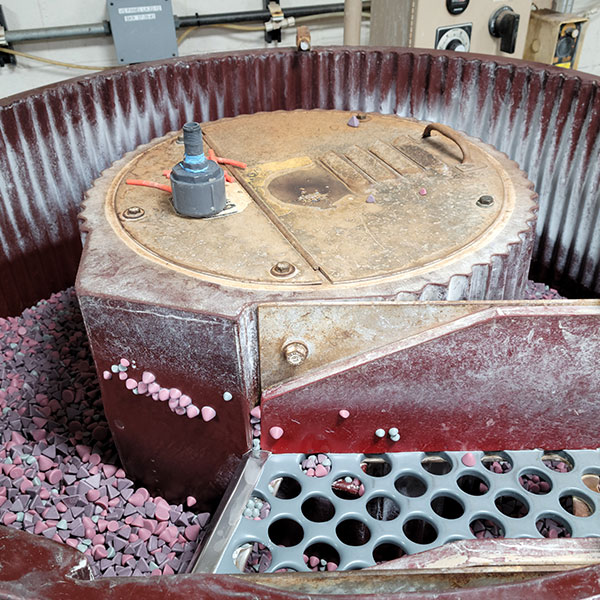
- Citric Acid Passivation:This process provides a stain-resistant finish to stainless steel metals. We can also provide other cleaning options on a customized basis utilizing other standards
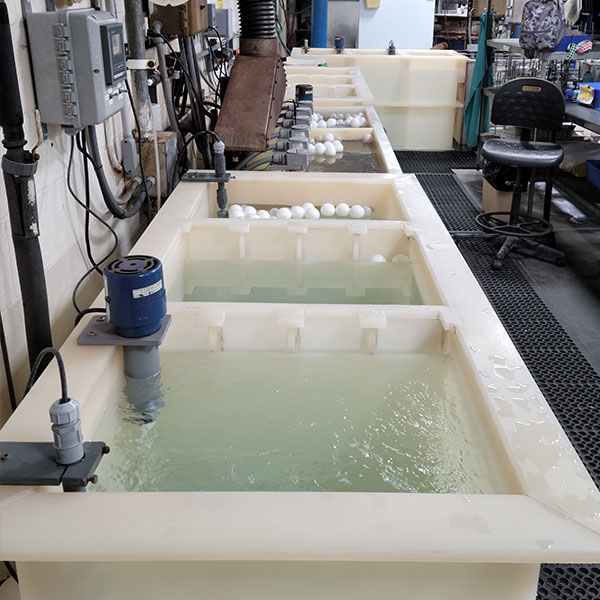
- Electropolishing:We electropolish 300 stainless steel, 400 stainless steel, 17-4 and 17-7
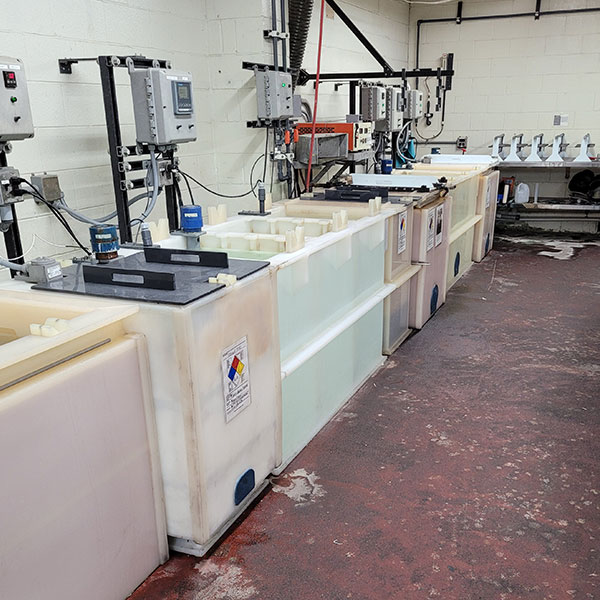
- Bead Blasting/Abrasive Blasting:Bead blasting is used to create a more uniform finish to parts and blades that need to have a more matte finish to them. We currently offer glass and aluminum oxide finishing. Glass is for finishing and aluminum oxide is to help clean any residue off the parts.
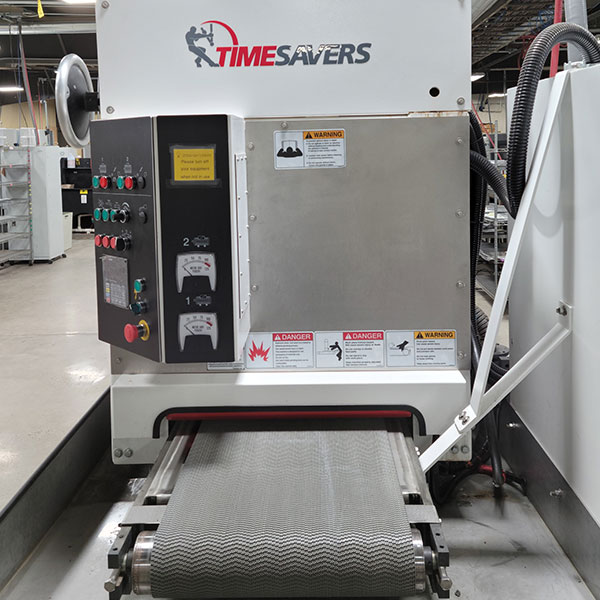
Environmentally Controlled Assembly and Packaging:
Cleanrooms are classified from 1 to 9, with ISO 1 being the cleanest and ISO 9 being the least clean; the most common classes are ISO 7 and ISO 8. Based on a yearly survey conducted by a third party, our Environmentally Controlled Packaging Area is in compliance with an ISO Class 8 cleanroom. We currently use this area to package finished medical devices in preparation for sterilization.
Our packaging capabilities include but are not limited to: Tyvek pouches, Tyvek lids with thermoformed trays, custom boxes, and heat-sealed polybags. Validated sealing processes are available in our Environmentally Controlled Packaging Area. We also can produce custom labeling with linear and matrix (two-dimensional) barcodes for internal and external packaging.
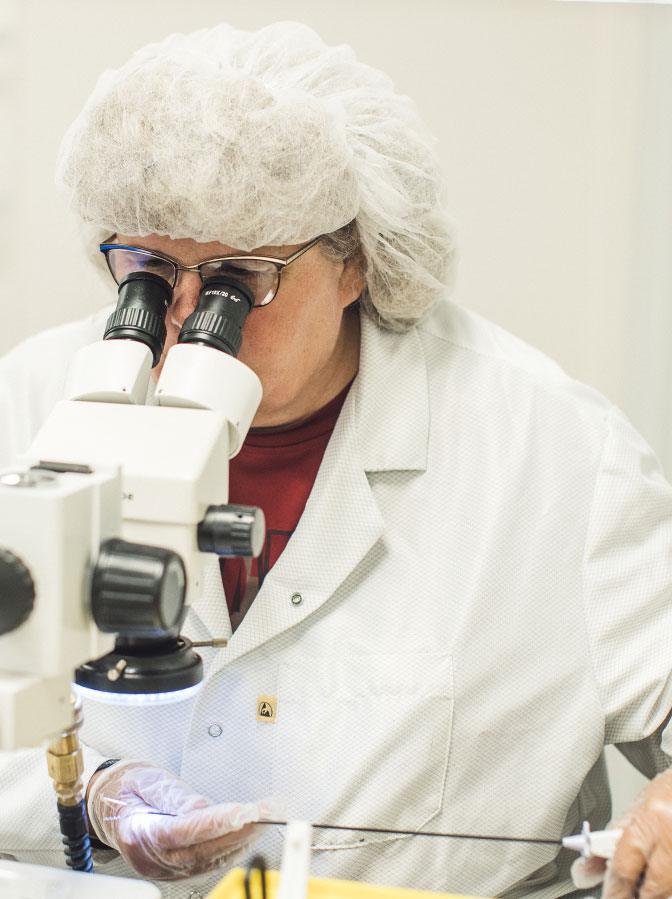
Contact our Manufacturing Team today to learn how we can help you with heat treating services, cleanroom services, and clean room manufacturing packaging.
Contact Us